2024/07/16
インタビュー
「人で守る」 から「仕組みで守る」時代
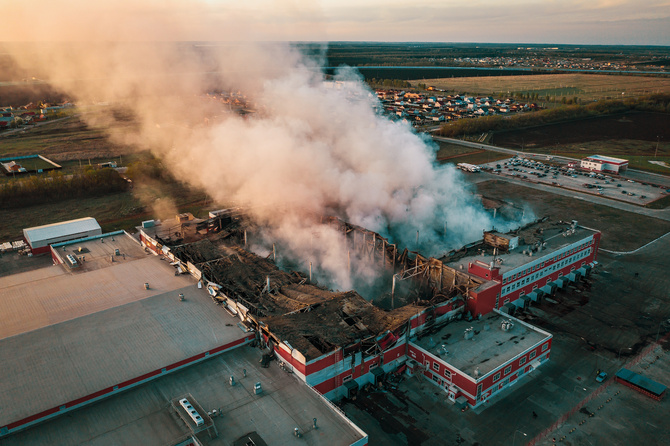
工場やプラント、倉庫の設備やシステムを最適に動かす制御・運用技術(OT:オペレーショナル テクノロジー)のリスクは情報セキュリティーだけにとどまらない。安全面の技術が伝承されていないなど、ほかにも課題は多いという。横河デジタルソリューションビジネス事業本部の田嶋信太郎氏に日本のOTにおける課題を聞いた。
ーー生産工場や物流などの制御システムが抱える OT リスクが注目されている。
生産工場などを管理、運営する上で、重要な要素にProductivity(生産性)、Quality(品質)、Cost(価格)、Delivery(納期)、Safety(安全)がある。以前は高品質な製品(Q)を、短い納期(D)で、低コスト(C)に生産することが求められていたが、現在は効率性と安全性を含め、それぞれの頭文字をとって、PQCDSと呼ばれている。
Iotに代表されるテクノロジーがOTで注目され、導入が進んでいる。だからこそ、OTセキュリティー対策が重要だと言われている。だが、そういったOTリスクはあくまでテクノロジーを活用できる、PQCDに関連する分野のみ。SのSafetyに関しては、デジタル化が困難だ。最大の課題は安全を確保する技術が伝承されず、生産過程のリスクが高まる可能性があることだ。
ーーなぜ生産過程でリスクが高まっているのか?
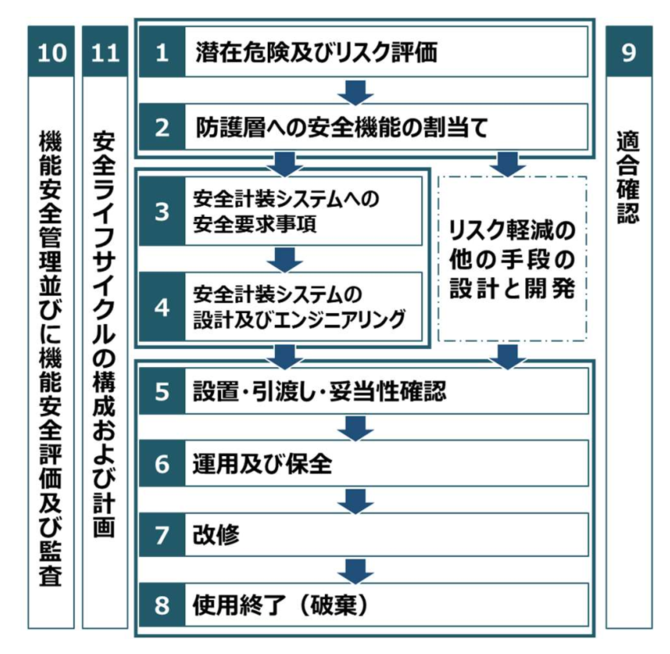
これまでの日本の工場は高い技術に支えられ、生産過程の安全性が確保されてきた。それは、一つに日本では転職が少なく、人材の流動性が低いために長期間にわたり工場で生産に関わり、経験を積めたことが大きい。海外なら流動性が高いために、人の入れ替わりが激しく、人という資源を頼りにできず仕組みで守るしかなかった。だからこそ、IEC61511のような国際規格を活用して、工場の安全性を確保してきた。
ただ、近年の日本は多くの技術者が定年退職し、生産過程の危険性の把握やインシデントが発生した際の対応に精通している人が少なくなっている。テクノロジー進展や効率化が進み、以前に比べて生産に関わる人材が減っている影響も少なくない。
残された担当者の中でも、生産過程の安全性を確保するすべを把握しているのは一部のみ。なぜなら、すべを取得するには、どうしても経験という長い時間が不可欠だからだ。これまでは、特別な対応をしなくても工場の機能的安全性を維持できてきたが、これから10年、20年先の人材不足を考えると人材の優秀さが仇になったとも言える。
時間の流れは止められない。このまま施設の老朽化が進み、人材不足が続けば、生産過程での安全性が保証されなくなる。我々の業界では、一度でも火災や爆発事故を起こすと、工場はそのままでは再稼働できない。一発でアウトになるために「ワンストライクアウト」と表現し、生産過程の安全を確保する重要性を説いてきた。現在残っている人材からの知識や経験の、早急な伝承が求められている。
- keyword
- オペレーショナルテクノロジー
- 横河デジタル
インタビューの他の記事
おすすめ記事
-
自社の危機管理の進捗管理表を公開
食品スーパーの西友では、危機管理の進捗を独自に制作したテンプレートで管理している。人事総務本部 リスク・コンプライアンス部リスクマネジメントダイレクターの村上邦彦氏らが中心となってつくったもので、現状の危機管理上の課題に対して、いつまでに誰が何をするのか、どこまで進んだのかが一目で確認できる。
2025/04/24
-
-
常識をくつがえす山火事世界各地で増える森林火災
2025年、日本各地で発生した大規模な山火事は、これまでの常識をくつがえした。山火事に詳しい日本大学の串田圭司教授は「かつてないほどの面積が燃え、被害が拡大した」と語る。なぜ、山火事は広がったのだろうか。
2025/04/23
-
リスク対策.com編集長が斬る!今週のニュース解説
毎週火曜日(平日のみ)朝9時~、リスク対策.com編集長 中澤幸介と兵庫県立大学教授 木村玲欧氏(心理学・危機管理学)が今週注目のニュースを短く、わかりやすく解説します。
2025/04/22
-
帰宅困難者へ寄り添い安心を提供する
BCPを「非常時だけの取り組み」ととらえると、対策もコストも必要最小限になりがち。しかし「企業価値向上の取り組み」ととらえると、可能性は大きく広がります。西武鉄道は2025年度、災害直後に帰宅困難者・滞留者に駅のスペースを開放。立ち寄りサービスや一時待機場所を提供する「駅まちレジリエンス」プロジェクトを本格化します。
2025/04/21
-
-
大阪・関西万博 多難なスタート会場外のリスクにも注視
4月13日、大阪・関西万博が開幕した。約14万1000人が訪れた初日は、通信障害により入場チケットであるQRコード表示に手間取り、入場のために長蛇の列が続いた。インドなど5カ国のパビリオンは工事の遅れで未完成のまま。雨にも見舞われる、多難なスタートとなった。東京オリンピックに続くこの大規模イベントは、開催期間が半年間にもおよぶ。大阪・関西万博のリスクについて、テロ対策や危機管理が専門の板橋功氏に聞いた。
2025/04/15
-
BCMSで社会的供給責任を果たせる体制づくり能登半島地震を機に見直し図り新規訓練を導入
日本精工(東京都品川区、市井明俊代表執行役社長・CEO)は、2024年元日に発生した能登半島地震で、直接的な被害を受けたわけではない。しかし、増加した製品ニーズに応え、社会的供給責任を果たした。また、被害がなくとも明らかになった課題を直視し、対策を進めている。
2025/04/15
-
-
生コン・アスファルト工場の早期再稼働を支援
能登半島地震では、初動や支援における道路の重要性が再認識されました。寸断箇所の啓開にあたる建設業者の尽力はもちろんですが、その後の応急復旧には補修資材が欠かせません。大手プラントメーカーの日工は2025年度、取引先の生コン・アスファルト工場が資材供給を継続するための支援強化に乗り出します。
2025/04/14
※スパム投稿防止のためコメントは編集部の承認制となっておりますが、いただいたコメントは原則、すべて掲載いたします。
※個人情報は入力しないようご注意ください。
» パスワードをお忘れの方